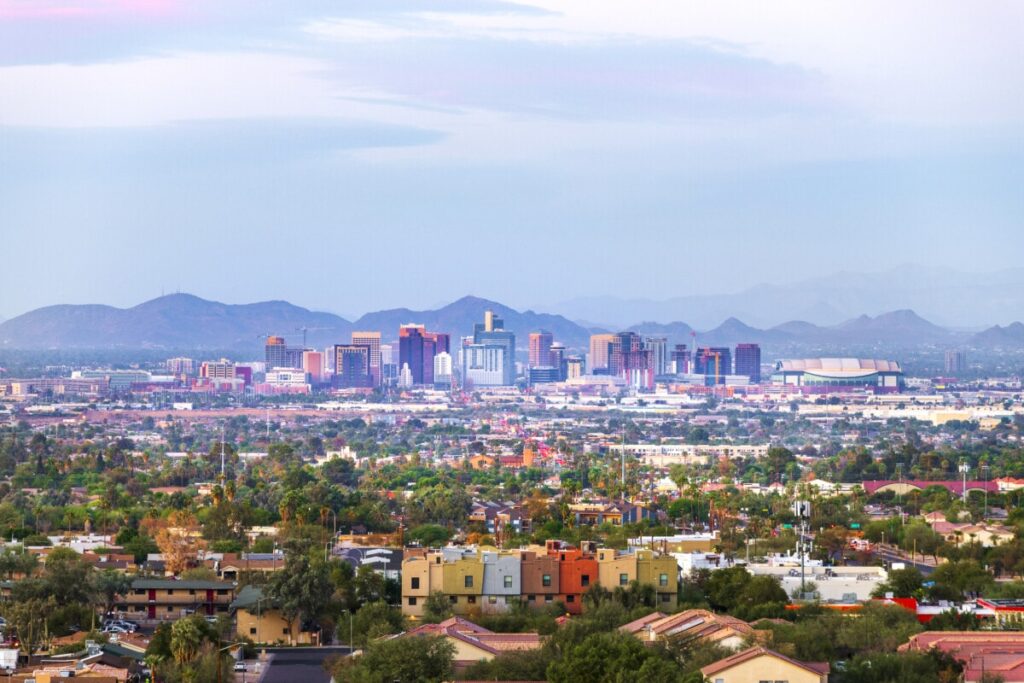
Industrial epoxy flooring, often overshadowed by traditional concrete or tile solutions, carves its niche with unparalleled durability and versatility. This unique character sets it apart in the vast world of industrial flooring solutions, offering a distinct experience that distinguishes industrial epoxy flooring as a category in its own right. Key types of industrial epoxy flooring systems include Self-leveling Epoxy, Epoxy Mortar Floors, Anti-static Epoxy, and Epoxy Flake Floors, each known for their distinct advantages.
Single Grain Epoxy, though less common, stands out as well, offering a smoother but equally robust choice for industrial environments. Diving deeper, each type of industrial epoxy flooring system presents its own set of benefits, application techniques, maintenance requirements, and recommendations for specific industrial settings. The following sections will explore these aspects in detail, providing a richer understanding of what makes industrial epoxy flooring a preferred choice for enhancing strength, durability, and aesthetics in industrial spaces worldwide.
What is epoxy flooring?
Epoxy flooring is a resilient and versatile coating applied over concrete floors to provide a durable, high-performance surface. It consists of a two-part system: a resin and a hardener, which, when mixed, create a robust material that adheres strongly to its substrate. This flooring solution is renowned for its ability to withstand heavy industrial use, resist chemical spills, and ease of maintenance, making it an ideal choice for factories, warehouses, and commercial spaces seeking long-lasting floor protection and aesthetic enhancement.
Why choose epoxy for industrial spaces?
Epoxy flooring stands out as the premier choice for industrial environments due to its high resistance to wear, making it ideal for areas subjected to heavy machinery and foot traffic. Its chemical and stain resistance ensures that it can withstand harsh substances without degradation, preserving the integrity of the floor. Additionally, epoxy flooring enhances safety by offering slip resistance, reducing the risk of accidents in the workplace.
This combination of durability, maintenance ease, and safety features positions epoxy as a superior flooring solution for industrial spaces looking for long-term, cost-effective, and reliable surface protection.
High resistance to wear
Epoxy flooring is renowned for its exceptional durability, capable of enduring the constant movement of people and machinery, making it an optimal choice for high-traffic industrial environments.
Chemical and stain resistance
Its impermeable surface resists various chemicals, oils, and stains, ensuring that spills can be cleaned easily without leaving lasting damage, thus maintaining the floor’s integrity over time.
Enhances safety with slip resistance
Epoxy floors can be tailored with textured finishes to reduce slipping hazards, significantly enhancing workplace safety by minimizing the risk of accidents related to falls.
Epoxy’s role in strength and durability
Epoxy flooring contributes significantly to the strength and durability of industrial spaces by forming a strong bond with concrete substrates, ensuring a long-lasting, resilient surface. Its superior impact and abrasion resistance protect floors from daily wear and tear, heavy machinery, and harsh chemicals, making it an indispensable solution for maintaining the structural integrity and appearance of industrial environments.
Strong bond with concrete substrates
Epoxy flooring establishes a robust bond with concrete, creating a seamless and durable surface that withstands the rigors of industrial activity and prolongs the lifespan of the floor.
Superior impact and abrasion resistance
Its composition provides exceptional resistance to impacts, abrasions, and heavy loads, safeguarding the floor against damage and ensuring it remains in top condition even in demanding environments.
Types of industrial epoxy flooring systems
Industrial epoxy flooring systems come in various types, each designed to meet specific needs and applications. Self-leveling epoxy floors provide a smooth, seamless surface ideal for areas requiring high standards of cleanliness and aesthetics. Epoxy mortar floors are recognized for their maximum durability, making them suitable for environments subjected to extreme conditions.
Anti-static epoxy systems are essential in spaces where electronic safety is a priority, preventing static electricity buildup. Lastly, epoxy flake floors offer a decorative finish while still maintaining the resilience and strength characteristic of epoxy, adding an aesthetic dimension to functional spaces. Each type embodies a unique blend of performance and design, catering to the diverse requirements of industrial flooring.
Self-leveling epoxy for smooth surfaces
Self-leveling epoxy creates a flat, seamless surface, perfect for areas needing a clean, attractive look without compromising on durability.
Epoxy mortar floors for maximum durability
Epoxy mortar systems offer the utmost in strength, making them ideal for industrial environments that experience severe wear and tear, such as manufacturing plants and garages.
Anti-static epoxy for electronic safety
Designed to prevent static electricity buildup, anti-static epoxy flooring is crucial in spaces where electronic components are handled or stored, reducing the risk of static discharge.
Epoxy flake floors for decorative finish
Epoxy flake flooring combines robust epoxy with colored flakes, providing a visually appealing yet strong surface suitable for commercial and retail spaces looking to enhance aesthetics along with functionality.
Installation process of epoxy flooring
The installation of epoxy flooring is a meticulous process that begins with surface preparation and cleaning, ensuring the concrete substrate is free of dust, dirt, and any contaminants. This is followed by the application of a primer to enhance adhesion between the concrete and the epoxy layer. Subsequently, the epoxy coating is applied, a step that requires precise mixing and application techniques to achieve a uniform and durable surface.
Finally, the curing process allows the epoxy to harden and bond to the substrate, a critical phase that determines the floor’s longevity and resilience. Each step in the installation process is vital to ensuring the epoxy flooring performs to its full potential in industrial settings.
Surface preparation and cleaning
Proper surface preparation is crucial, involving thorough cleaning to remove any debris, oils, or existing coatings, ensuring a clean slate for epoxy application.
Primer application for better adhesion
A primer is applied to the prepared surface to enhance the bond between the concrete and the epoxy, setting the foundation for a durable, long-lasting floor.
Epoxy coating application techniques
The epoxy coating is meticulously applied using specific techniques to ensure even coverage and optimal thickness, contributing to the floor’s overall strength and aesthetic appeal.
Curing process and time frames
After application, the epoxy must undergo a curing process, which varies in time depending on the product and environmental conditions, solidifying the coating’s bond to the substrate and achieving its final hardness and resistance properties.
Maintenance of epoxy floors
Maintaining epoxy floors is straightforward, requiring only routine cleaning with mild detergents to keep the surface looking pristine. It is important to avoid harsh chemicals and abrasives that can damage the epoxy coating. For high-traffic areas, periodic resealing may be necessary to preserve the floor’s integrity and appearance.
This simple yet effective maintenance regimen ensures the longevity and durability of epoxy flooring in industrial environments, making it a cost-effective solution for businesses seeking a reliable and easy-to-care-for flooring option.
Routine cleaning with mild detergents
Routine maintenance of epoxy floors involves cleaning with mild detergents to remove dirt and spills, preserving the floor’s glossy finish without compromising its integrity.
Avoiding harsh chemicals and abrasives
To maintain the epoxy floor’s durability and appearance, it is crucial to avoid the use of harsh chemicals and abrasive cleaning tools that can erode the surface and diminish its protective qualities.
Periodic resealing for high-traffic areas
In areas subjected to heavy foot or machinery traffic, periodic resealing of the epoxy floor may be necessary. This process rejuvenates the floor’s resilience, ensuring its longevity and sustained performance.
Long-term benefits of epoxy in industrial spaces
Epoxy flooring offers significant long-term benefits for industrial spaces, including cost-effectiveness and lifecycle savings due to its durability and low maintenance requirements. It also plays a crucial role in improving workplace safety and morale by providing a slip-resistant and visually appealing environment. Moreover, the aesthetic versatility and design options available with epoxy coatings allow for customized solutions that can enhance the overall appearance of a facility.
These advantages make epoxy flooring a strategic investment for businesses looking to optimize their operational efficiency, safety, and workplace aesthetics.
Cost-effectiveness and lifecycle savings
Epoxy flooring is a cost-effective solution for industrial spaces, offering significant lifecycle savings due to its long-lasting durability and minimal maintenance needs, reducing the overall expense over time.
Improving workplace safety and morale
By providing a slip-resistant surface and contributing to a cleaner, more organized environment, epoxy flooring significantly enhances workplace safety and boosts employee morale, creating a more productive and secure workspace.
Aesthetic versatility and design options
With a wide range of colors and finishes available, epoxy flooring offers unparalleled aesthetic versatility, allowing businesses to customize their floors to fit their brand identity or operational needs, thus improving the visual appeal of industrial spaces.
Frequently Asked Questions:
- What is industrial epoxy flooring, and why is it preferred for industrial spaces?
Industrial epoxy flooring is a robust flooring solution made from epoxy resin that is specifically designed for use in industrial environments. It’s preferred for industrial spaces due to its exceptional durability, chemical resistance, and seamless finish. The epoxy resin creates a strong bond with the underlying concrete substrate, forming a tough surface that can withstand heavy machinery, foot traffic, spills, and other harsh conditions commonly found in industrial settings. Additionally, it’s customizable, offering options for slip resistance, anti-static properties, and decorative finishes.
- How durable is industrial epoxy flooring compared to other flooring options?
Industrial epoxy flooring is one of the most durable flooring options available, surpassing many traditional flooring materials such as concrete, tile, or vinyl. Its high compressive strength and resistance to impact, abrasion, chemicals, and moisture make it exceptionally durable, even in the most demanding industrial environments. With proper installation and maintenance, industrial epoxy flooring can last for decades without showing signs of significant wear and tear.
- Can industrial epoxy flooring withstand heavy machinery and equipment?
Yes, industrial epoxy flooring is engineered to withstand the weight and movement of heavy machinery and equipment commonly found in industrial settings. Its high compressive strength and impact resistance make it ideal for environments with forklifts, pallet jacks, and other heavy machinery. Additionally, epoxy flooring can be reinforced with additional layers or additives to enhance its load-bearing capacity and durability in areas with particularly heavy traffic or equipment.
- What are the installation requirements for industrial epoxy flooring?
The installation of industrial epoxy flooring typically involves several steps, including surface preparation, primer application, epoxy coating, and topcoat application. Surface preparation is critical to ensure proper adhesion and a smooth finish, often involving concrete grinding or shot blasting to remove contaminants and create a profile for the epoxy to bond to. The specific installation requirements may vary depending on the condition of the substrate, the desired thickness of the flooring, and any additional features such as chemical resistance or anti-slip properties. Professional installation by experienced epoxy flooring contractors is recommended to ensure optimal results and longevity.
- Are there any special considerations for the maintenance of industrial epoxy flooring?
While industrial epoxy flooring is relatively low-maintenance compared to other flooring options, there are some considerations to keep in mind. Regular cleaning with a mild detergent and water is typically sufficient to keep the surface clean and free of debris. Spills should be promptly cleaned up to prevent staining or damage to the epoxy coating. Depending on the specific requirements of the facility, periodic resealing or topcoat application may be necessary to maintain the integrity of the flooring and ensure long-term performance. Additionally, heavy machinery and equipment should be equipped with proper flooring protection to prevent scratching or gouging of the epoxy surface. Regular inspections and maintenance checks can help identify any issues early and prevent costly repairs or replacements down the line.